I’ve been doing functional ABS and ASA lately and had a couple very annoying warpage spots. One was a total failure. (We won’t talk about the other 3 failures that were wet out-of-the-box Bambu ASA…)
The X1C is definitely nice, but the all aluminum-and-glass side panelling has a sometimes-unwanted side effect: thermal conduction.
The aluminum sides are so conductive that they do not allow the chamber temp to go above 40C, even after a couple hours of heat soaking the build plate at 100C before starting an ABS print.
Enter: One random bath towel. doesn’t look like much but just covering the three sides with a thin layer means it’s good enough insulation to get the chamber up to 50C now! And the ABS parts look better than ever- every C counts.
Thanks for taking the time to type out a reply. Using my hot end as my chamber thermistor (hot end off, hot end fan max), after soaking for ~1 hour, my chamber tops out around 45c. My printer does have the filter + 2 extra bed fans, but other than that it’s a fairly vanilla 2.4, complete with acrylic panels. Your post inspired me to work on panel mounts for the ACM panels I’ve had next to the printer for a few months.
How did your foam tape fail? Thankfully, I haven’t had that happen to me yet. I’m going extra wide on the foam tape to put the radiant bubble insulation on the inside of the panels. This is the real reason why I’ve been putting off mounting them - I needed to modify the mounts I’ve been previously using. I’m also not sure if the magnets will hold the extra weight, so I might need to get… creative.
What thermistor are you using for your chamber?
I tend to do what you do - find a brand of filament I like and stick with it. That said, so far I’ve only used Polymaker’s polylight ASA. What was your experience with Polymaker vs Matter3d? Polymaker puts 3kg spools up for very cheap every once in a while, but I’m happy to pay more for an easier to print filament.
Yeah the acm insulated better than I expected, probably the pu layer? As for the tape It just kinda fell off the wall, it’s not the best surface, old concrete board I think, has a rough surface, was for powerbar cables and the power bar itself, was super secure when I put them up but they came down about 6 months later, they’re all up with wall anchors now. The foam on the panels hasn’t failed yet, used different stuff on the doors and its adhesive kinda seeped out, not happy about it though, been meaning to do something about the doorgap too so figure I’ll do all at once. I need to do some panel mounts changes too,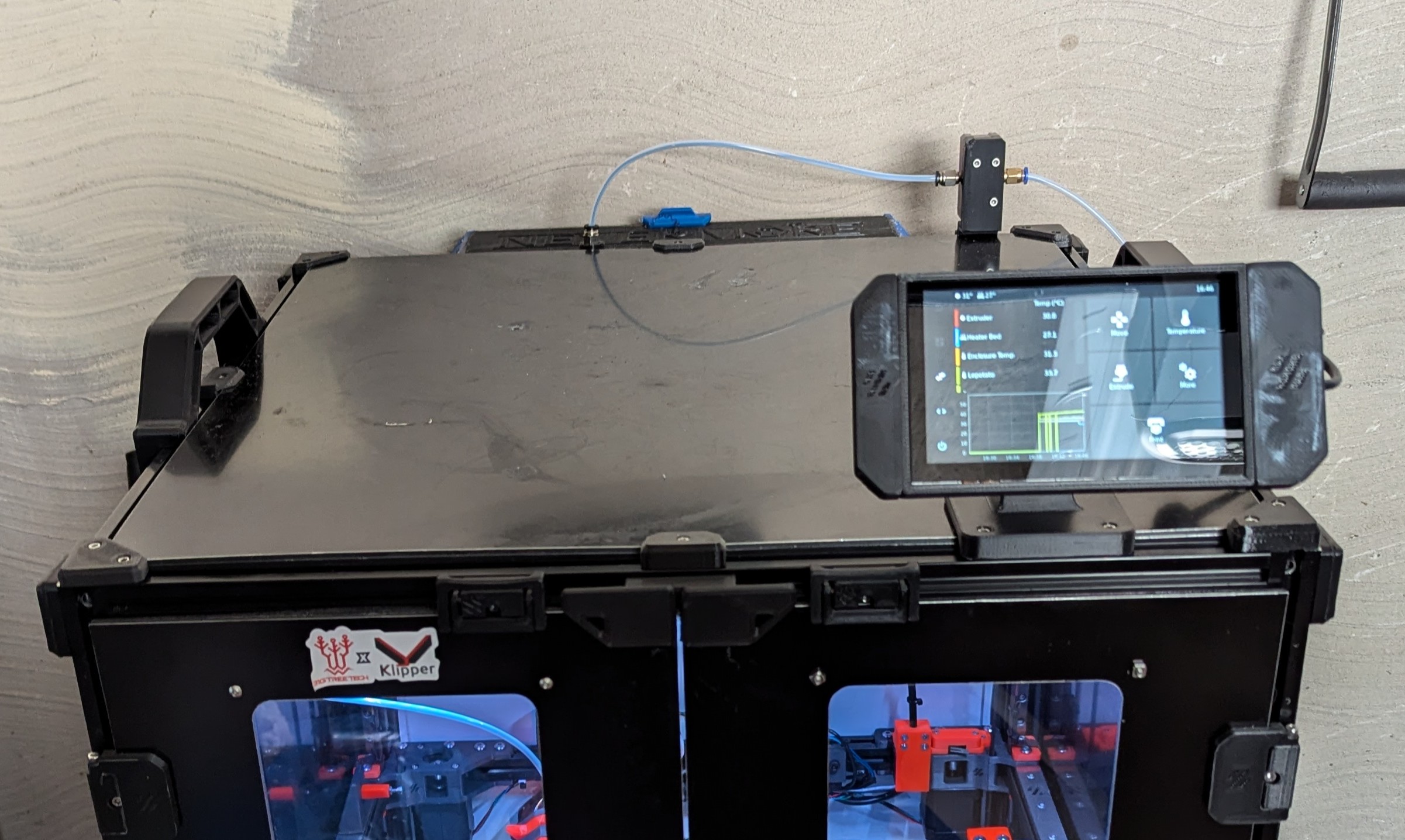
I moved the touchscreen to the top of the printer because I was tired of hunching over, I ran the cables under the panel and added some extra foam tape around it and used an extra clip to squish it all together, it works but want something better
I have a bunch of spare hotend thermistors, used one of them, this printer’s using a pt1000 anyhow so was fine using the one I swapped out.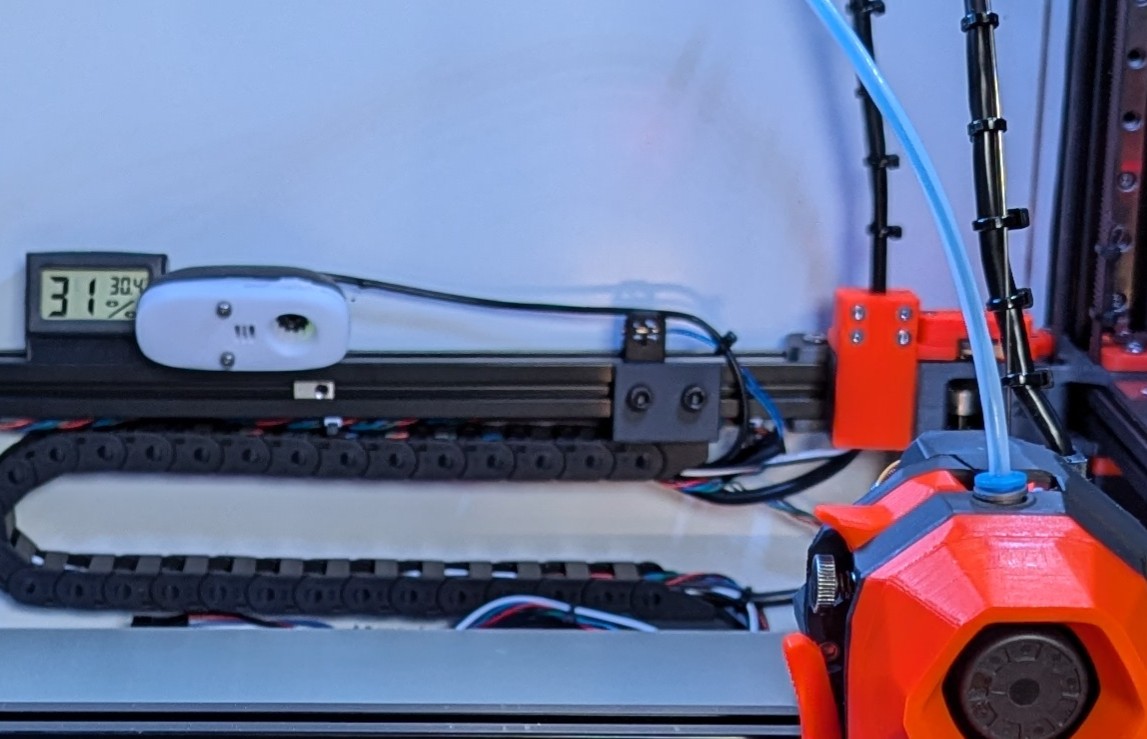
I use a reference more than anything.
I’ve gone through a bunch of polylite abs, which prints pretty well, but it stinks, may actually be one of the stronger smelling abs I’ve printed with. That’s the immediate difference, the Matter3D stuff has way less smell, almost none actually, need to practically stick your face right up against the door for a bit. Print wise, I’ve just used the extrusion multiplier I use for all abs so not tuned a profile yet, kept up with a decent print speed and it can go hotter (if I recall wants 235-270), quality is solid, very dry out of the bag, does come on plastic spools though.